- November 3, 2021
- Posted by: Tom Richert
- Categories: Culture, Innovation, Leadership
By Bryan Wahl and Tom Richert
Large cost savings are possible with an effective application of lean practices in building design. The following chart illustrates the expected project cost for the Lakewood Family Health Center development through the course of design and construction. The integrated team developed a lean culture that successfully applied a target value delivery methodology, reducing the cost significantly during the design phase without sacrificing building program or aesthetics. The cost was further reduced during construction and using a lean construction workflow methodology the team shortened the construction schedule by five months. The chart was prepared by Bostwick Design Partnership and presented at the 2019 Lean Construction Institute Congress.
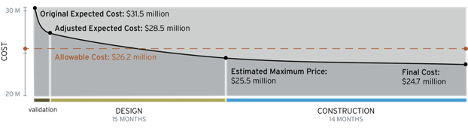
The process of delivering building projects begins with an understanding of why the community needed the building. Situated in an urban environment at a prominent and busy intersection, the Lakewood Family Health Center is designed in response to the surrounding buildings and pedestrian environment. The appearance and building organization were carefully composed to provide clarity for the patient and visitor experience. The project replaced a dated, less effective facility. It features a 24-hour emergency department, imaging services, multi-specialty, and family medicine – all with the latest technologies at the time.
The highly efficient plan allows for large exterior windows around the perimeter while keeping the number of corridors at a minimum. The access to daylight enhances the waiting and exam spaces, reduces stress, and guides visitors and patients through the building and fills a critical role within the City of Lakewood by providing accessible, efficient, and immediate care. This building is a resource to sustain the health and wellness of the community. Despite its importance to the community the business case did not support the expected cost of the facility based on benchmark building costs in the region. Given recent positive results with lean construction coaching on other projects the client decided to move forward with the project utilizing lean design and construction practices, confident the team would find a way to reduce project costs without compromising the function or aesthetics of the building.
Why was this Team Successful?
First, the team created a culture of commitment, transparency and performance solidified by a set of agreements that committed the team to a lean approach. A Team Development process was used to create an inclusive forum to establish and maintain teamwork fundamentals. During this project, team members became problem solving innovators who, regardless of their role, are committed to the mission of the project in every respect. The project conditions of satisfaction guided the Team’s decisions. Team meetings were cooperative, comprehensive proactive strategies were developed and productivity was optimized. This integrated team maximized the Owner’s desired outcomes.
Second, the team created a set of guiding principles to inform decisions and actions.
- Allow for the transformation of healthcare delivery by creating a space that will foster relationships between the patients and care givers.
- Promote growth and development in the City of Lakewood.
- Support the needs of patients and healthcare workers for the next 15 years by providing flexibility with the space, sustainable materials, and dependable systems.
- Employ the lean delivery model to add value through the design and construction of the building.
- Develop and document processes that will serve as a baseline for future client projects.
- Foster positive relationships.
Third, deployed a range of lean tools. The Lakewood FHC team implemented lean practices to drive waste from all project phases including conceptual design, team selection, design, construction, and close-out. Practices included the Target Value Delivery, Last Planner System®, Choosing By Advantages Decisionmaking, and A3 Management. The learning environment created a platform for consistent, continuous team improvement.
Fourth, the team established protocols for colocation that supported collaborative work. During design the construction manager co-located in the architect’s office and the mechanical and electrical trade contractors co-located with the MEPT Engineer, creating real time constructability review and cost understanding. Guided by the design phase plan, trade contractors worked directly in the design team’s building information model, eliminating the need for redundant shop drawings and independent model development. The team came together weekly during construction to actively drive solutions.
Fifth was the application of lean practices during construction, which had an immediate positive impact to the project costs. The team used small-zone batch flow, equipment sharing, and productivity monitoring to accelerate the construction timeline without adding personnel or working overtime.
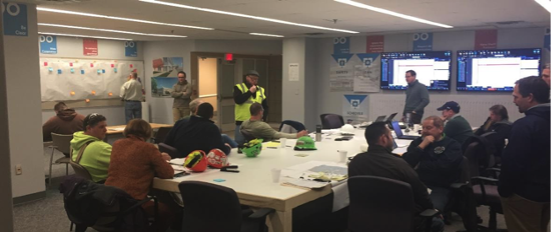
Project Outcomes
The success of this project demonstrates that lean practices are effective at reducing project costs and accelerating project schedules while designing and constructing a quality facility. A factor that distinguishes this project from less successful lean projects is the team’s focus on cultivating and sustaining a positive, team-oriented work culture. This focus on culture is vitally important as it supports the clear and transparent conversations that need to happen across a project team for lean to succeed.
About the Authors
Bryan C. Wahl, AIA, Principal, Bostwick Design Partnership,
Lead Architect for the Lakewood Family Health Center Project
I enjoy putting things together, creating stories, and teaching others throughout the design process to reach their goals. The design process inspires me to create, going beyond the building and shaping the environment. As a good listener, I absorb and analyze information first and then translate it into a design. By leading conversations through which designs are conceptualized, refined, and developed detail is uncovered and clarity is gained to achieve desired outcomes.
Tom Richert, Principal, RisingTerrain LLC,
Lean Coach for the Lakewood Family Health Center Project
Organizations far too often invest in productivity at the expense of people. It’s impossible to achieve and sustain high levels of productivity solely focusing on work processes. People matter more than process. I enjoy helping workplace teams understand that productivity is an expression of the healthy connections between people who work together. It’s fantastic to see people embrace ever higher standards for themselves and others through advancing their professional development in a team context.
Leave a Reply
You must be logged in to post a comment.